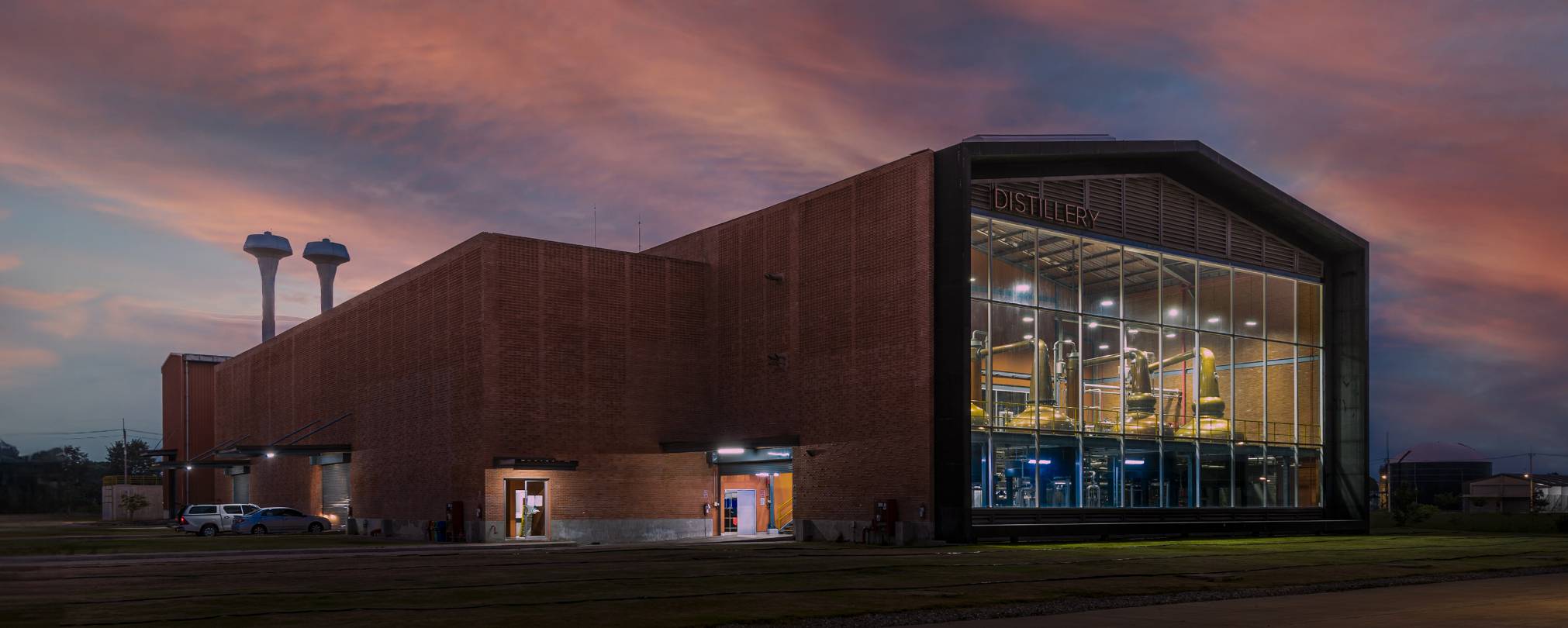
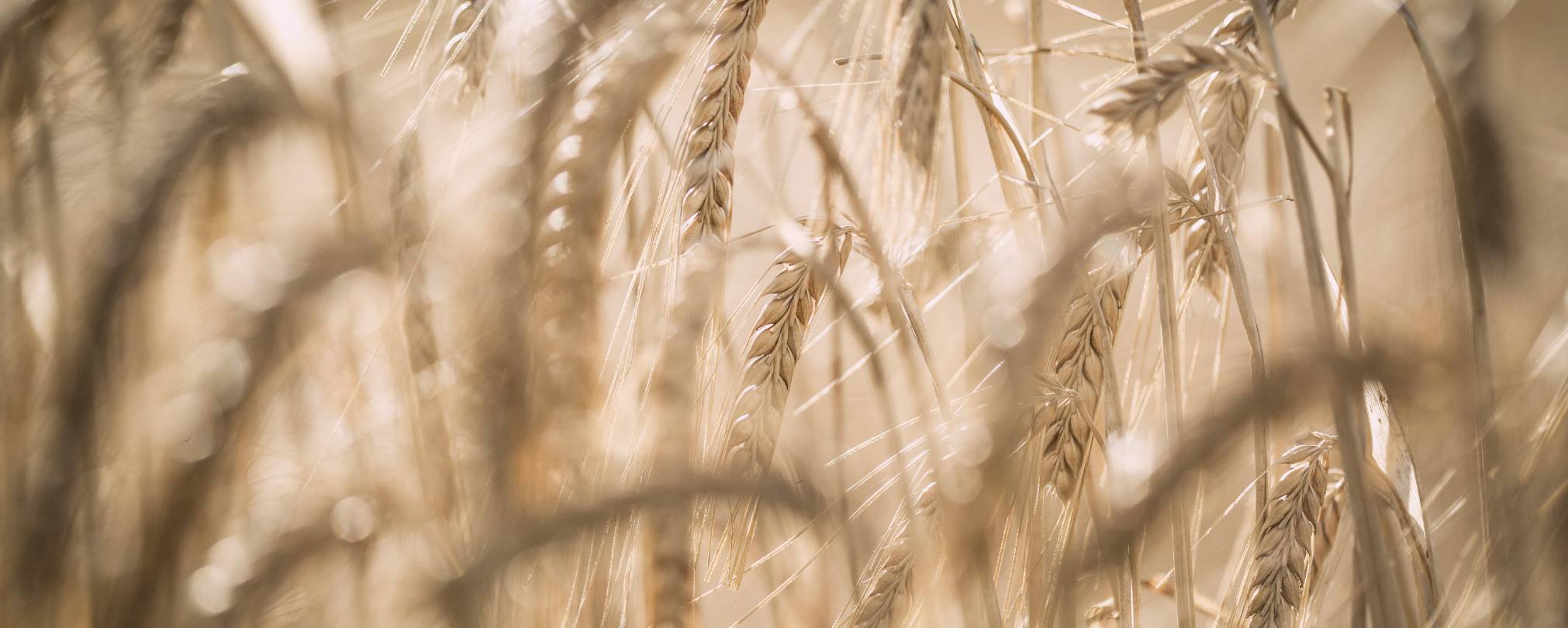

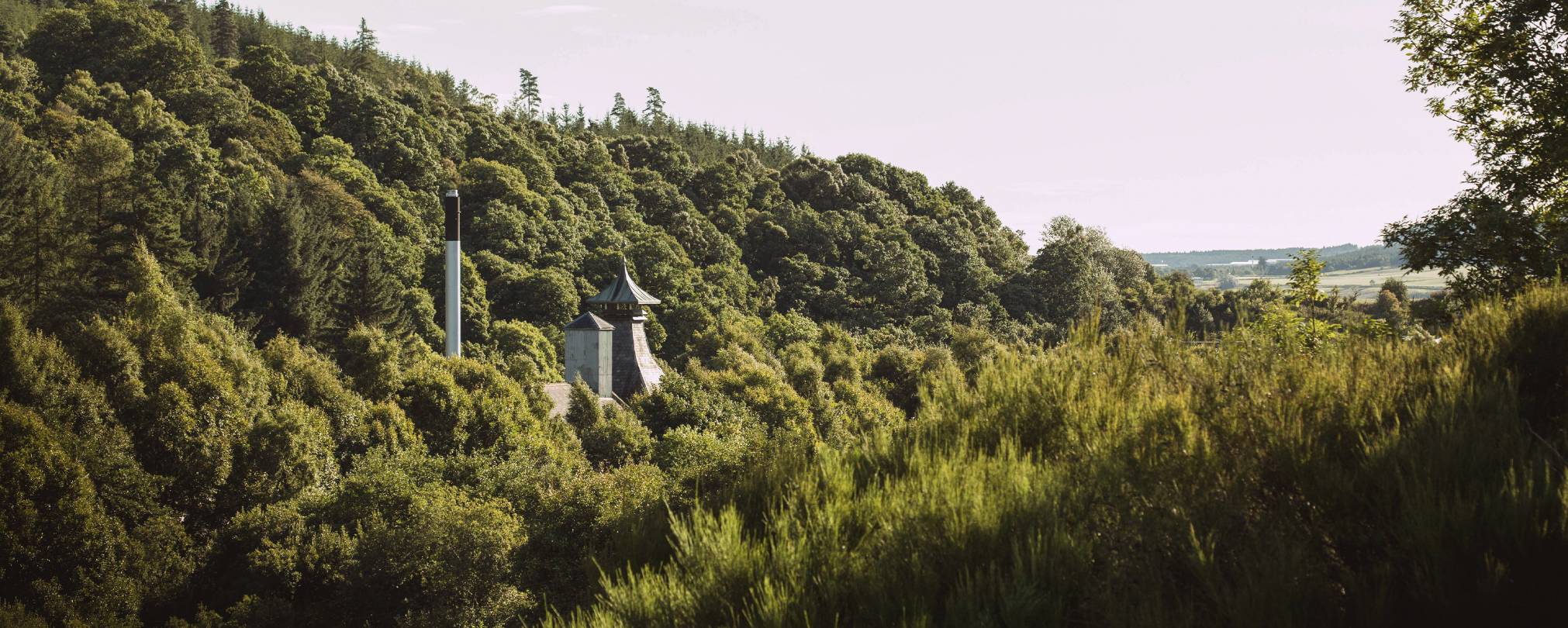
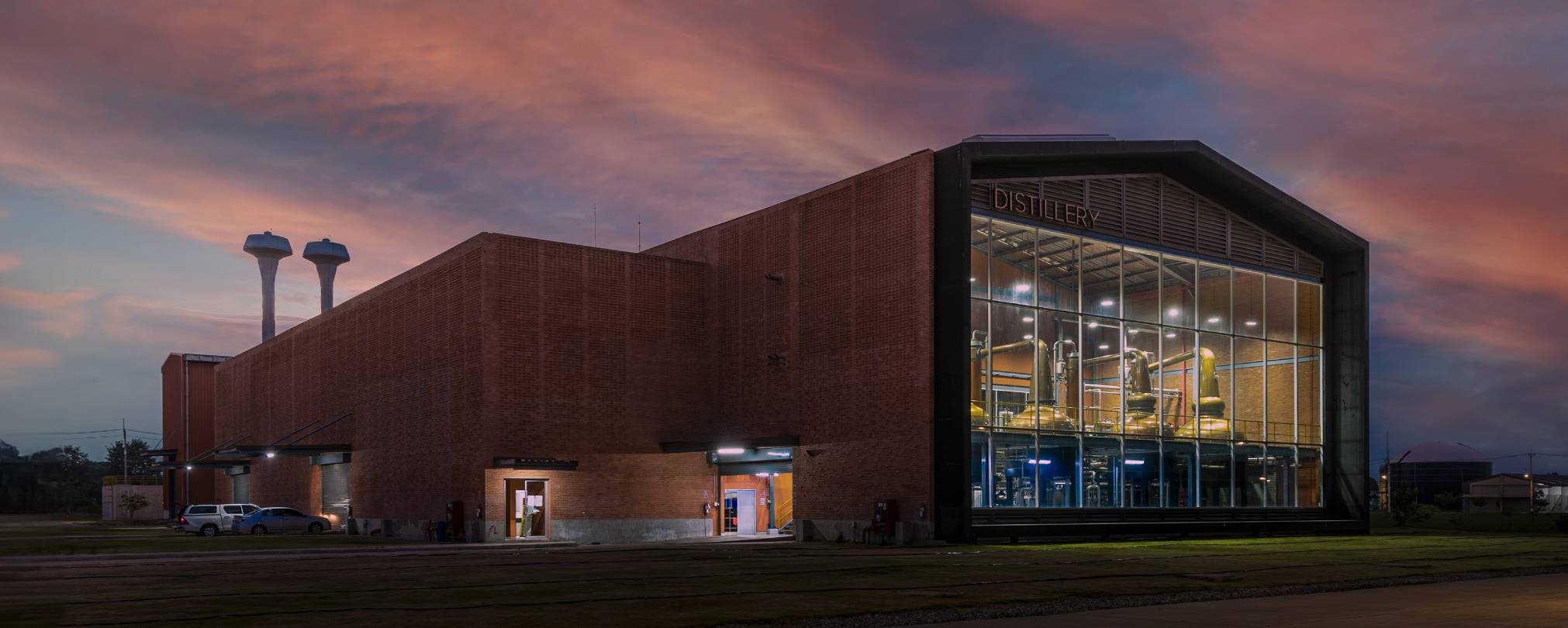

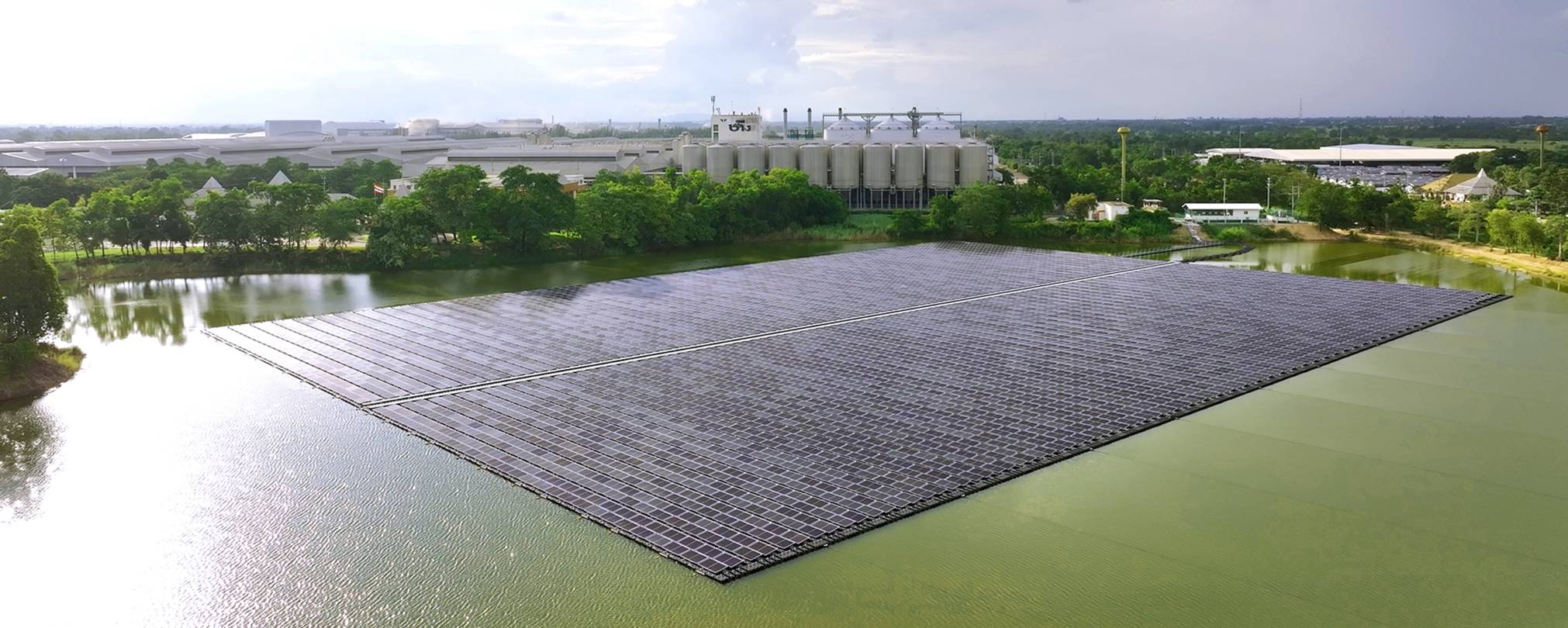
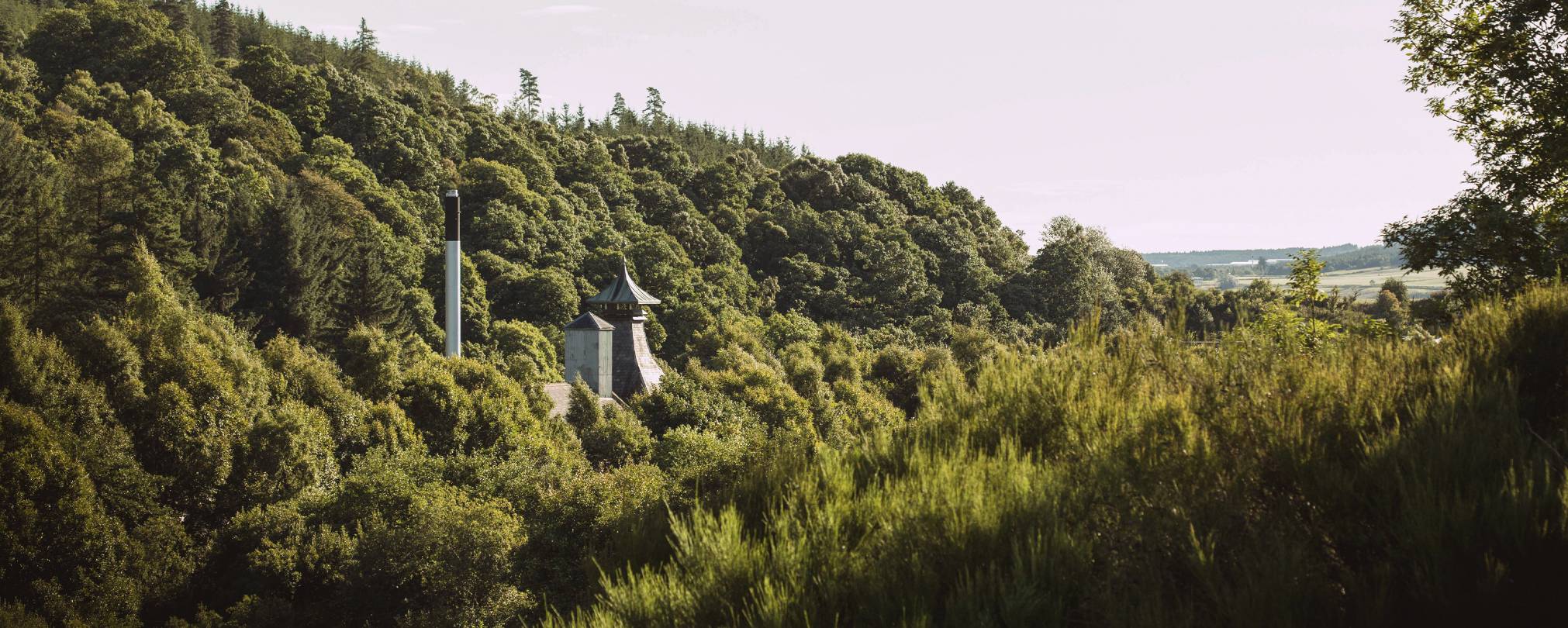
30
โรงกลั่นและโรงงานผลิตสุรา
30
โรงงานผลิตเบียร์
31
โรงงานผลิต
เครื่องดื่มไม่มีแอลกอฮอล์
ภาครัฐ-เอกชน ร่วมพลังศรัทธาแห่งแผ่นดิน สานต่อพระราชปณิธานพระมหากษัตริย์ไทย จัดงาน “สืบสานงานพ่อ ต่อยอดทุนเล่าเรียนหลวงสำหรับพระสงฆ์ไทย”
เพื่อสืบสานพระราชปณิธานในการทำนุบำรุงพระพุทธศาสนาของพระมหากษัตริย์ไทย ที่จะจัดขึ้นระหว่างวันที่ ๒ – ๔ กรกฎาคม ๒๕๖๘ ณ หอประชุมพุทธมณฑล จังหวัดนครปฐม
“ROYAL JAZZ FOR THE CHAIPATTANA FOUNDATION” จัดแสดงอย่างยิ่งใหญ่ เฉลิมพระเกียรติ 70 พรรษาสมเด็จพระกนิษฐาธิราชเจ้า กรมสมเด็จพระเทพรัตนราชสุดาฯ สยามบรมราชกุมารี
ขับขานบทเพลงพระราชนิพนธ์ในพระบาทสมเด็จพระบรมชนกาธิเบศร มหาภูมิพลอดุลยเดชมหาราช บรมนาถบพิตร เพื่อเฉลิมพระเกียรติเนื่องในวาระ 70 พรรษา สมเด็จพระกนิษฐาธิราชเจ้า กรมสมเด็จพระเทพรัตนราชสุดาฯ สยามบรมราชกุมารี
คุณฐาปน เปิดวิสัยทัศน์ “การพัฒนาอย่างยั่งยืนเพื่อฝ่าวิกฤติภัยพิบัติทางธรรมชาติ”
คุณฐาปน สิริวัฒนภักดี ประธานเจ้าหน้าที่บริหาร บริษัท ไทยเบฟเวอเรจ จำกัด (มหาชน) ร่วมเป็นเกียรติปาฐกถา หัวข้อ “การพัฒนาอย่างยั่งยืนเพื่อฝ่าวิกฤติภัยพิบัติทางธรรมชาติ” ในงานปาฐกถาเกียรติยศ “เวฬา ณ จุฬาลงกรณ์ฯ”
สมเด็จพระกนิษฐาธิราชเจ้า กรมสมเด็จพระเทพรัตนราชสุดา ฯ สยามบรมราชกุมารี เสด็จเปิดนิทรรศการ ศิลปกรรมช้างเผือก ครั้งที่ 14
นิทรรศการ ศิลปกรรมช้างเผือก ครั้งที่ 14 ภายใต้หัวข้อ “น้ำกับความเปลี่ยนแปลง” ซึ่งเป็นเวทีการประกวดงานศิลปะสำหรับการสร้างสรรค์ผลงานศิลปะ ที่แสดงถึงแก่นแท้ความคิดผ่านงานเสมือนจริง และงานศิลปะรูปลักษณ์
ไทยเบฟ สนับสนุนการติดตั้งสถานีโทรมาตรอัตโนมัติ ๗๒ สถานี เพื่อเฉลิมพระเกียรติพระบาทสมเด็จพระเจ้าอยู่หัว เนื่องในโอกาสพระราชพิธีมหามงคลเฉลิมพระชนมพรรษา ๖ รอบ ๒๘ กรกฎาคม ๒๕๖๗
บริษัท ไทยเบฟเวอเรจ จำกัด (มหาชน) สนับสนุนการติดตั้งสถานีโทรมาตรอัตโนมัติ ๗๒ สถานี ให้กับ มูลนิธิอุทกพัฒน์ ในพระบรมราชูปถัมภ์ และสถาบันสารสนเทศทรัพยากรน้ำ (องค์การมหาชน) (สสน.)